Ceramic mug sublimation time and temp: An Expert Guide
Contents
- 1 Ceramic mug sublimation time and temp: An Expert Guide
- 2 1. Introduction to Sublimation Printing
- 2.1 2. Science of Sublimation: How It Works
- 2.2 3. General Sublimation Parameters
- 2.3 4. In-Depth Comparison of Mug Press Machines
- 2.4 5. Oven Sublimation: Pros, Cons, and Techniques
- 2.5 6. Advanced Factors Affecting Sublimation Quality
- 2.6 7. Safety Protocols and Machine Maintenance
- 2.7 8. Troubleshooting Common Sublimation Issues
- 2.8 9. Case Study: Optimizing Workflow for High-Volume Production
- 2.9 10. Future Trends in Sublimation Technology
- 2.10 11. Conclusion
1. Introduction to Sublimation Printing
Sublimation printing is a process where heat and pressure transform solid dye particles into gas, allowing them to bond permanently with polymer-coated surfaces. For ceramic mugs, this method produces vibrant, long-lasting designs. This guide dives deep into optimizing time and temperature parameters, explores equipment variations, and addresses common challenges.
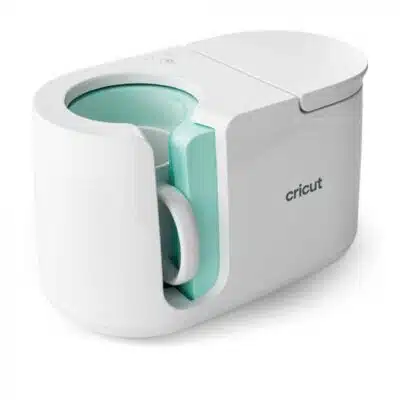
2. Science of Sublimation: How It Works
Understanding the science behind sublimation ensures better control over results:
- Phase Change: Dye sublimation ink turns from solid to gas at 150–200°C, bypassing the liquid phase.
- Polymer Coating: Mugs must have a specialized polyester or polymer coating to trap gaseous ink.
- Pressure’s Role: Even pressure (40–50 psi) ensures contact between the transfer paper and mug surface.
3. General Sublimation Parameters
3.1 Temperature Guidelines
- Standard Range: 180–200°C (356–392°F).
- Below 180°C: Incomplete sublimation causes faded or blotchy prints.
- Above 200°C: Risk of glaze cracking, yellowing, or scorched transfers.
- Adjustments for Specific Cases:
- Dark-Colored Mugs: Increase temperature by 5–10°C to enhance ink penetration.
- Textured Surfaces: Raise temperature by 5°C to compensate for uneven heat distribution.
3.2 Time Settings
- Standard Duration: 120–150 seconds (2–2.5 minutes).
- Thin-Walled Mugs (11 oz): 120–130 seconds.
- Thick-Walled Mugs (15 oz+): Extend to 160–180 seconds.
- Preheating: Always preheat the machine to the target temperature before inserting the mug to avoid thermal shock.
3.3 Pressure Requirements
- Optimal Pressure: 40–50 psi (pounds per square inch).
- Adjustable Machines: Use higher pressure for curved surfaces (e.g., travel mugs).
- Fixed Machines: Ensure the mug fits snugly in the press to maintain even pressure.
4. In-Depth Comparison of Mug Press Machines
Different brands use unique heating technologies and pressure systems. Below is an expanded analysis:
4.1 Microtec ProPress Series
- Temperature Range: 185–195°C.
- Time: 120–140 seconds.
- Heating Mechanism: Dual ceramic heating plates with PID temperature control.
- Key Features:
- Auto-Shutoff: Prevents overheating.
- Versatility: Compatible with 11–15 oz mugs and tumblers.
- Best For: High-volume production with consistent results.
4.2 Printful CraftMaster
- Temperature Range: 175–190°C.
- Time: 130–160 seconds.
- Heating Mechanism: Quartz tubes for rapid warm-up (2–3 minutes).
- Key Features:
- Energy Efficiency: 30% lower power consumption than competitors.
- Compatibility: Works with plates, coasters, and 11–13 oz mugs.
- Best For: Small businesses prioritizing eco-friendly operations.
4.3 TradeKey T8
- Temperature Range: 190–205°C.
- Time: 110–135 seconds.
- Heating Mechanism: Quartz heaters with turbo fan for rapid heat distribution.
- Key Features:
- Speed: Reaches 180°C in 30 seconds.
- Precision: Ideal for intricate designs due to ±2°C temperature accuracy.
- Best For: High-detail artwork and time-sensitive projects.
4.4 Hix AutoPress Vertical
- Temperature Range: 180–200°C.
- Time: 140–160 seconds.
- Heating Mechanism: Vertical ceramic plates with adjustable pressure.
- Key Features:
- Pressure Control: Manual tuning (30–60 psi) for textured mugs.
- Capacity: Fits mugs up to 20 oz.
- Best For: Irregularly shaped or oversized mugs.
4.5 Epson SurePress
- Temperature Range: 170–195°C.
- Time: 135–155 seconds.
- Heating Mechanism: Hybrid ceramic and quartz system.
- Key Features:
- Smart Sensors: Auto-adjust time and temperature based on mug thickness.
- Software Integration: Syncs with design software for batch processing.
- Best For: Tech-driven studios with automated workflows.
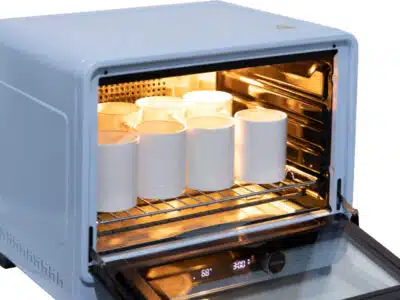
5. Oven Sublimation: Pros, Cons, and Techniques
While professional mug presses are ideal, ovens can be used with caution.
5.1 Equipment Setup
- Oven Types: Convection ovens are preferable for even heat distribution.
- Temperature Calibration: Use an external oven thermometer to verify accuracy.
- Accessories:
- Heat-Resistant Tape: Secure transfer paper to the mug.
- Rotating Tray: Promotes uniform heating (e.g., pizza oven turntables).
5.2 Time and Temperature Adjustments
- Temperature: Set to 190–200°C (374–392°F).
- Time: Extend to 180–210 seconds due to slower heat penetration.
- Positioning: Place mugs in the center of the oven, 6–8 inches apart.
5.3 Limitations of Oven Use
- Inconsistency: Hotspots and airflow issues lead to uneven prints.
- Safety Risks: Higher fire hazard due to prolonged high heat.
- Labor-Intensive: Requires constant monitoring.
6. Advanced Factors Affecting Sublimation Quality
6.1 Mug Material and Coating
- Polymer Coating Types:
- Standard Coating: Suitable for basic designs.
- High-Temp Coating: Withstands up to 210°C for dark mugs.
- Coating Thickness: 20–30 microns is ideal; thinner coatings may cause ink bleed.
6.2 Environmental Conditions
- Humidity:
- High Humidity (>60%): Slows ink drying; use dehumidifiers.
- Low Humidity (<30%): Increases static, risking misaligned transfers.
- Altitude: Higher altitudes lower boiling points, requiring slight temperature adjustments.
6.3 Design Complexity
- Full-Color Graphics:
- Increase temperature by 5°C and extend time by 20 seconds.
- Use 200–220 DPI resolution for sharpness.
- Gradient Effects:
- Print at 190°C to prevent color banding.
- Use a 10% higher ink density.
6.4 Transfer Paper Quality
- Paper Types:
- Lightweight (60–70 gsm): Faster ink release but prone to tearing.
- Heavyweight (90–100 gsm): Better for complex designs but requires higher heat.
- Storage: Keep paper sealed in a cool, dry place to prevent moisture absorption.
7. Safety Protocols and Machine Maintenance
7.1 Safety Practices
- Heat Protection: Use gloves rated for 250°C.
- Ventilation: Install exhaust fans to disperse fumes from sublimation ink.
- Fire Safety: Keep a CO2 fire extinguisher nearby.
7.2 Machine Maintenance
- Daily:
- Wipe heating plates with isopropyl alcohol.
- Check pressure alignment using a blank test mug.
- Monthly:
- Calibrate temperature sensors with a laser thermometer.
- Inspect wiring for fraying or damage.
- Annual:
- Replace heating elements in high-use machines.
8. Troubleshooting Common Sublimation Issues
8.1 Faded Colors
- Causes: Low temperature, short time, or expired ink.
- Solutions:
- Increase temperature by 5°C and retest.
- Replace sublimation ink older than 6 months.
8.2 Ghosting/Blurred Edges
- Causes: Mug movement during pressing or low pressure.
- Solutions:
- Secure the mug with silicone wraps.
- Increase pressure to 50 psi.
8.3 Glaze Cracking
- Causes: Thermal shock from rapid cooling.
- Solutions:
- Let the mug cool inside the press for 2–3 minutes.
- Avoid placing hot mugs on cold surfaces.
8.4 Ink Bleeding
- Causes: Excessive heat or over-saturated paper.
- Solutions:
- Reduce temperature by 5°C.
- Use a lint roller to remove excess ink from transfer paper.
9. Case Study: Optimizing Workflow for High-Volume Production
- Scenario: A mid-sized print shop producing 500 mugs daily.
- Challenges: Inconsistent colors, machine downtime.
- Solutions:
- Upgraded to Microtec ProPress with dual heating zones.
- Implemented a 10-minute preheating routine.
- Reduced defects by 40% and increased output by 25%.
10. Future Trends in Sublimation Technology
- Smart Machines: IoT-enabled presses with remote monitoring.
- Eco-Friendly Inks: Water-based sublimation inks reducing VOC emissions.
- 3D Sublimation: Printing on curved and irregular surfaces using flexible heaters.
11. Conclusion
Mastering sublimation on ceramic mugs requires balancing time, temperature, and equipment capabilities. Whether using a budget-friendly oven or a high-end mug press, attention to detail in material selection, environmental factors, and maintenance ensures professional results. Always conduct test prints and document adjustments for repeatable success.